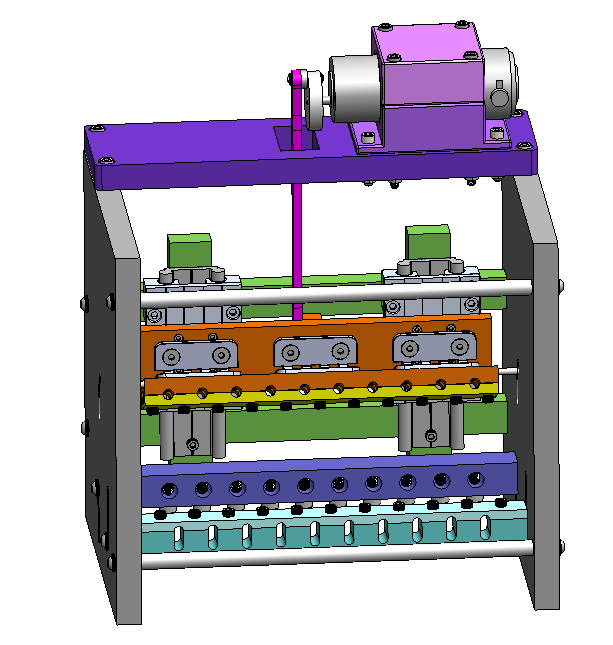
Currently, there isn’t yet a way to provide visual stimuli to both eyes simultaneously and individually to see which side of the brain has stronger results (contralateral vs ipsilateral).
To design and build visual stimulus goggles for ultra-high field (7 Tesla) MRI for high resolution studies of functional organization of visual cortex using SOLIDWORKS, Arduino, and EAGLE. The goggles must be electromagnetically compatible to a high-res 7T MRI, compact, able to control color, able to adjust luminance, provide motion stimulus, and binocularly adjustable.
After working with my boss on the technical requirements of electronics that are 7T MRI compatible,
I started to brainstorm some ideas. Then, I designed the goggle frame using SOLIDWORKS. The goggle
frames include strain relief clamps for
the wires, as well as a slit for a diffuser. The goggles were curved in a way to help provide full
coverage around the patient’s head - cleanable, hygienic padding will be added.
I searched online for compact, non-magnetic LEDs with a voltage and current in our range.
After finalizing all of our electrical components, the schematic and PCB board design were made in
EAGLE. The PCB board was then sent out to be manufactured.
After receiving the PCB boards from the manufacturer, the next step was to secure the LEDs, inductors,
chokes, capacitors, and wires onto the PCB. I initially tried to use a soldering iron, but it
proved to be tricky as it was difficult to establish a secure connection between teh PCB and the
component and also hard to avoid melting the electrical components. I eventually tried the solder cream and
an oven to secure the components properly. I was able to use a multimeter to check for a complete circuit and
to troubleshoot any issues that arose. After some troubleshooting, I was able to start
testing the goggles with an Arduino code generated by the previous project owner and the first version of these
7T MRI goggles were created!
The first version of the 7T MRI goggles have been prototyped!
The motor in the existing anatomical bend fixture causes instability to the fixture, thus affecting the motion of the pump, efficiency, accuracy, and continuous motion.
To revise the existing anatomical bend fixture (inherited from a previous co-op)and create an ergonomic design of the anatomical bend fixture with multiple analyses involving, ease of use, occupancy of space, sample size, and so forth.
After working with my mentor on the technical and design requirements of the fixture,
I performed a shape analysis on how the heart pump would move in the current version
of the fixture compared to clinical outcomes. Following the shape analysis, I started
to brainstorm some design change ideas and areas of improvement.
I designed various ways to stabilize the motor wobble using SOLIDWORKS. After testing each design,
I was able to come to a decision on which design was best suited to stabilize the motor wobble.
I also designed a way to incorporate a small shaft and make a linkage to avoid frictional wear
issues between componentes. After finalizing all of the components, I was able to get these
parts sent out for quick manufacturing and test the fixture in-house.
The linear bend cyclic bend anatomical fixture successfully accomplished its design goals. The fixture no longer has a motor wobble, performs the full motion, and has been updated and documented into the system to be incorporated into the next round of verification testing.
Copyright © Jen Yeo 2024 |